Ever wondered how the twang of a Stratocaster, or the growl of a Les Paul guitar could be replicated, or even bettered? A crucial part of the answer lies hidden within the pickups, those unsung heroes responsible for the electric guitar’s distinctive tone. As a seasoned engineer and practicing luthier, I can tell you with conviction that building your own guitar pickup winder can be a defining step towards mastering this complex instrument.
It was 1994 when I first dared to venture beyond simply playing the guitar and delve deeper into its construction. Fueled by a passion for the instrument and a relentless quest to understand what made it tick, I found myself entranced by the guitar’s pickups. Those little metallic bars could magically transform mere string vibrations into soulful melodies that echoed around the auditorium. My pursuit for that perfect tone led me to venture into winding my own pickups.
The journey from player to luthier is a thrilling one, marked by revelation and occasional frustration. The decision to construct a guitar pickup winder at home was revolutionary, a moment that fundamentally changed my relationship with the instrument. Suddenly, I held the power to control the voice of my beloved guitar. A newfound respect was born for the luthier’s craft and the intricate engineering behind a guitar pickup.
In the following pages, we’ll explore every detail about building a guitar pickup winder. From understanding the basic mechanics, dissecting different parts, to exploring varied designs – we’ll tackle it all. This ultimate guide is a culmination of my experience, personally and professionally, over the years. It’s a tribute to the art of handmade pickups, and I hope it will inspire you to embark on a similar journey of discovery and creativity.
So, are you ready to give your guitar a voice that’s uniquely yours? Dive deep into the world of pickup winding, and let’s create some magic together.
The Mechanics of a Guitar Pickup Winder
Understanding Pickup Winder Parts
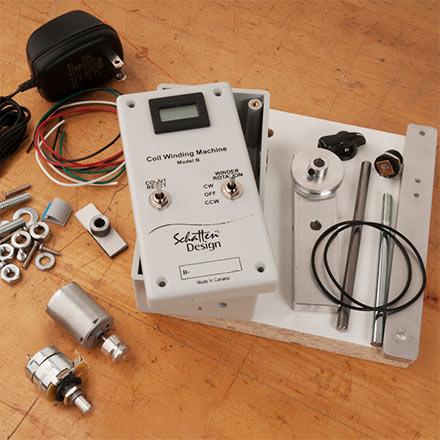
Stepping into the world of pickup winder parts, each component mirrors a member of an orchestra – each serves a specific function, but together, they create something truly special. Through my engineering journey, I’ve delved into each aspect, learning their unique voices and how they harmonize.
Undeniably, the heart of any winder is the pickup winder motor type. Like the conductor, it sets the pace and directs the operation. Its power and speed directly impact the precision of the winding, crucial to producing that perfect tone. Just remember, a higher speed doesn’t always equate to a better result – a symbiotic balance of power and control is key.
Next comes the winder traverse mechanism, akin to the first violin in our pickup orchestra. It guides the string back and forth across the pickup bobbin, ensuring evenly spaced windings, much like how the first violinist leads with melody. Make no mistake, a well-executed traverse mechanism can make the difference between a cacophonous or a euphonious output.
The elements above are just a few among several pickup winder parts contributing to the overall sound quality. They all matter; the spindle, the bobbin holder, and even the humble foot switch. Every tool plays its part contributing to the collective performance. Don’t overlook the seemingly inconspicuous contributors, their value is far from diminutive.
Understanding these elements is like deciphering a piece of music; the better you do it, the more fluid your performance will be. Comprehending their workings will guide you in your quest to create a winder that is truly your own, culminating in a guitar that sings in your unique voice.
Armed with this understanding, we are now ready to explore how these components come together in diverse winder designs. So let’s turn the page to the next exciting chapter.
Exploring Winder Designs
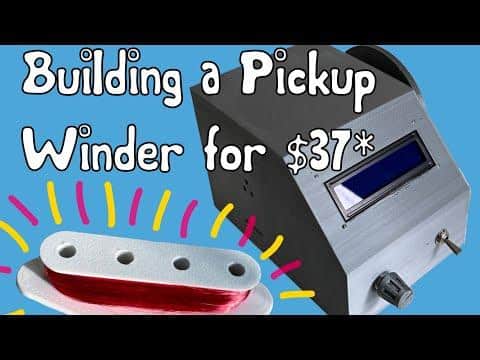
For me, the journey towards mastering lutherie was marked by the appreciations of how instrument design impacts the quality of the sound produced. The same is true for the mechanics of a guitar pickup winder. In particular, pickup winder design greatly influences the consistency and tone of the guitar pickups. As such, a deep understanding of different winder designs is essential.
The pickup winder design is so much more than just the physical structure; it incorporates the efficiency of operation, the level of control available to the user, and the precise delivery of wound pickup coils. My experience has taught me that the design significantly determines both the winder tension control and the performance of the pickup winder counter, which are fundamental aspects of the winding process.
Why is winder tension control so crucial? Perfect tension ensures the tautness of the wire being winded, influencing the quality of the pickup’s sound. The pickup winder counter, on the other hand, tracks the number of turns on the coil, enabling the user to recreate a pickup with surgical accuracy.
Design, then, becomes a critical variable in the winding equation. Everything from the elegance of operation to the precision of the sound—a poorly designed pickup winder can dramatically undermine the quality of your guitar pickups. Having explored numerous winder designs over the years, I can confidently state that a thoughtful design is integral to a successful guitar pickup winder.
As we proceed to examine how to build your own pickup winder, remember that it’s not just about putting pieces together. It’s about designing a winder that delivers precision, control, and excellent performance. This is the art and science of pickup winding, not just a subsection in this guide, but a foundational understanding that affects the entirety of the project.
DIY Pickup Winder
Building Your Own Pickup Winder
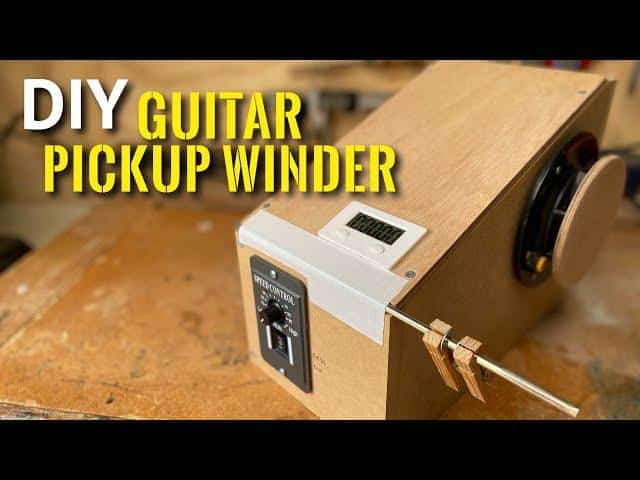
As we journey deeper into the world of DIY pickup winding, our next exciting chapter is to roll up our sleeves and build your own pickup winder. Going from reading about it to actually crafting one, adds an indescribable feeling of satisfaction to your guitar building experience.
A homemade pickup winding machine is not just a piece of gear; it’s an extension of your craft, a physical embodiment of your knack for DIY projects. Embarking on building your own pickup winder will certainly deepen your understanding of how these devices work, while giving you the liberty to customize and tweak the tool to your own specific needs.
Your journey begins by gathering the necessary components, which constitute the pickup winder kit. This includes the frame, motor, power supply, winding counter, and bobbin holder. I like to seek out quality components that ensure durability and give a solid performance while also striking a balance with costs.
For the frame, a good, sturdy material that can withstand the physical stresses of regular use is needed. I have used pieces of rectangular steel tubing in my builds for a good balance of cost and durability. The motor should be quiet, but powerful and able to offer a smooth operation at varying speeds. For me, low voltage DC motors have worked remarkably well.
The power supply is essential in determining the motor speed. I recommend a flexible supply that allows you to adjust voltage, hence controlling speed. A winding counter is critical to precision and replicability in your guitar builds. Accurate and easy-to-read counters make the job much easier. Finally, the bobbin holder is your interface for the pickup, and it’s crucial that your design holds the bobbin firm yet adjustable.
Once you have your components, the real fun begins, assembling it all together. It might seem like a daunting task, but take it from me, the joy of seeing all the pieces come together to form your personalized winder compensates for any complexities.
Through building your own pickup winder, you’re not only creating a significant tool, but you’re also continuing on a path of ongoing learning that is integral to the wonderful world of DIY guitar building. Up next, we’ll look at some projects and examples to keep your creative juices flowing. So, let’s move forward with the anticipation of crafting something truly special.
Projects and Examples
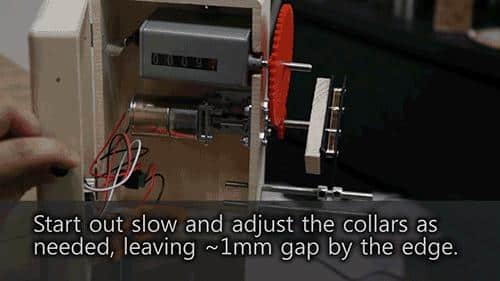
Chapter six brought us to the brink of breathing life into your very own DIY pickup winder. Now that we’ve covered the fundamentals and the building process, it’s time to delve into some specific pickup winder projects. Like I always say, there’s nothing more enlightening than applying theory to practice. I’ve undertaken countless pickup winder ventures and I’m thrilled to pass on the knowledge I’ve gained. Let’s go ahead and explore popular projects to get a sense of the journey you’re embarking on.
We’ll commence with an arduino pickup winder. An arduino pickup winder is a beneficial variant for those who enjoy combining music and technology. My development involved an Arduino UNO board, a stepper motor for winding precision, and a rotation counter to ensure the accurate number of wire turns. This project challenged me to integrate technological aspects into a traditional crafting project, which in turn, enhanced my understanding of the technical intricacies of pickup winders.
Another project that you might find intriguing would be a standard single coil pickup winder. This was one of my first attempts at pickup winder projects and provides a great entry-point for beginners. I used primary materials like a hand drill and PVC pipes to design the structure and a sewing machine foot pedal for speed control. This elementary project taught me the core principles of building a pickup winder and has been a solid foundation for my subsequent projects.
These projects have been valuable resources in my DIY journey. Each project, each attempt at improving upon my designs, has ingrained in me the realization that pickup winder projects are an art. It’s the art of combining creativity with technical know-how, the amalgamation of passion and precision. Learn the craft, make mistakes, do-overs and improvisations – that’s my advice. As we move to the next section, ‘The Art of Pickup Winding’, we’ll explore this artistic process further, concentrating on winding techniques and tips to master the craft.
The Art of Pickup Winding

Devising the blueprints for your pickup winder is an exciting process, but the real intrigue begins at the heart of it all – the winding. In my luthier journey, I’ve realized that coil winding is no less an art than playing the guitar itself. Drawing on both my luthier experience and engineering expertise, I am eager to delve into the science and the aesthetics of varied winding techniques and patterns, sharpening the sonics of your instrument.
It all begins with the bobbin winding. The bobbin is the skeleton on which we delicately wrap the pickup wire, a delicate handcraft that requires meticulous precision and patience. The choice of the wire gauge is vital. Winding delicate 43 or 44 gauge wire is like stringing a spider’s thread. Each layer of wire needs to lay flat and neat, ensuring there are no overlaps or maverick windings which could cause microphonics, detracting from the overall sound quality.
Did you know that the craft of pickup winding is as much an art as it is a science? Let’s unlock the secrets of this age-old technique and how it moulds the voice of your guitar. Every pickup winding technique has peculiarities which can, when executed skilfully, create uniquely beautiful sonic profiles. The total winding count has a direct influence on the pickup’s output and tone characteristics. Going low might just give you the reminiscent clarity of the vintage sound. Or, crank it up for some modern bite.
Here’s where the artistry comes in. As you control the winding speed on your pickup winding machine, you determine the winding pattern – from scatter winding to sectional winding and everything in between. A balanced execution of mixed patterns often leads to the most intriguing results. Yes, there’s audio physics involved, but for me, it’s entwined with the creative process, born not just from a place of knowledge but of intuition and feel.
Sometimes, many luthiers opt for an automatic coil winder. Indeed, it can produce perfect windings at a steady winder rpm, ensuring consistency. But machine-wound coils rarely capture the organic, nuanced tonal qualities that human touch can imbue. There’s something to be said about feel and instinct, the ability to sense when the wire needs to run a touch slower or the winding tension needs tweaking. It makes pickup winding a deeply personal, intimately human affair. Just like playing the music itself.
In my winding explorations, I have tried and tested numerous techniques, gauges, and machines. Some have led to spectacular sonic epiphanies, while others have kindled a forest of buzzing wires. These experiences only deepened my respect for this subtle art form and sparked in me an urge to further push the envelope of possibility.
Next, we embark on a practical journey to create a DIY pickup winder. And as we step into the world of soldering irons and magnet wires, remember; it’s your unique songwriting voice that we are putting the wind into. With every turn of the bobbin, we’re adding another note to your melody, another word to your lyrical narrative. And that’s the beauty of the art of pickup winding.
FAQs
What is a guitar pickup winder?
A guitar pickup winder is a device used to wind the wire coils found inside electric guitar pickups. The winding process of the coiled wire in these pickups is vital in creating the magnetic field necessary for the guitar pickups to function.
Why should I build my own guitar pickup winder?
By building your own guitar winder, you can ensure that the winding process meets your specific needs and preferences. It also makes for an interesting DIY project, offering you the satisfaction of creating your own guitar components. Lastly, it can help you save money in the long run, as opposed to buying pre-made guitar pickup winders.
What materials do I need to build a guitar pickup winder?
Some of the materials required include a motor, spool, RPM counter, pickup bobbin, wire, PVC tube, bearings, and a base to hold everything. You will also need various tools to assemble these parts, such as screwdrivers, a solder iron, a drill and bits etc.
How much does it cost to build a guitar pickup winder?
The cost to build a guitar pickup winder varies greatly depending on the specific components you choose to use. However, on average, you can expect to spend anywhere from $50 to $200, not considering the tools you may already have.
Conclusion
How does it feel to encompass this delightful journey of building a custom pickup winder? If you’re reading this, you’re probably sitting amidst your handmade pickups, pickup winder schematics, and maybe even some pickup winder software, soaking in the satisfaction of having built something with your own two hands. This guide has been put together with the intention of inspiring you, of providing valuable knowledge, and of imbuing you with the confidence to take on this endeavor. Because when you truly understand the inner workings of your instrument, you become closer to the music, more in tune with your own sound.
I hope these chapters have not only educated you about the mechanics, parts, designs and the overall art of pickup winding, but also about the very essence of DIY culture. Our shared passion for music isn’t just about the end product; it’s about the creation, the journey, the story we weave as we build our own instruments. Each project, whether it’s centered around handmade pickups or software-aided designs, has a story that adds a new chapter to our musical encounters.
To build your own guitar pickup winder is to form a direct, personal bond with your music – a bond that amplifies your art and resonates deep within you. So, as we conclude, I leave you not at the end of a guide, but at the beginning of your own unique, sonic adventure. I hope you have found this ‘Ultimate Guide’ not only instructive but transformative, lighting a path to new musical discoveries. Now, go forth and create your own one-of-a-kind sonic masterpiece.
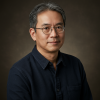